Speeds And Feeds Of Manual Lathes
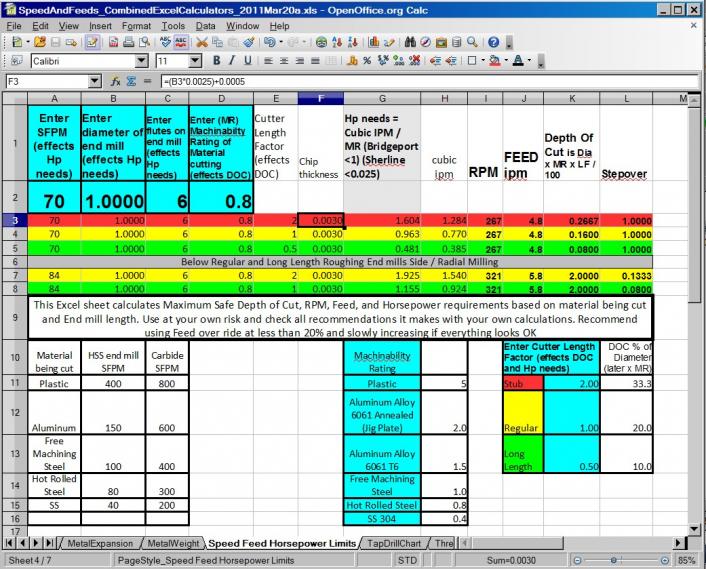
For aluminium, on a conventional lathe, rotational top speed of the mandrel will be a strong limitation, as for carbide tool cutting speed Vc reach 2000 m/min in. 9 Cleaning the Machine. 10 Unfinished Work. Conventional Milling. 12 Drilling and Drill Chucks. 13 Calculating Speeds and Feeds.
You should calculate RPM & Feed whenever machining with a Mill, Drill or Lathe. Experienced machinists often 'fudge it' while manual machining, making.
LATHE SPEEDS, FEEDS, AND DEPTH OF CUTS General operations on the lathe include straight and shoulder turning, facing, grooving, parting, turning tapers, and cutting various screw threads. Before these operations can be done, a thorough knowledge of the variable factors of lathe speeds, feeds, and depth of cut must be understood.
These factors differ for each lathe operation, and failure to use these factors properly will result in machine failure or work damage. The kind of material being worked, the type of tool bit, the diameter and length of the workpiece, the type of cut desired (roughing or finishing), and the working condition of the lathe will determine which speed, feed, or depth of cut is best for any particular operation. The guidelines which follow for selecting speed, feed, and depth of cut are general in nature and may need to be changed as conditions dictate. Cutting Speeds.
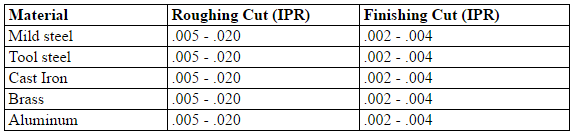
The cutting speed of a tool bit is defined as the number of feet of workpiece surface, measured at the circumference, that passes the tool bit in one minute. The cutting speed, expressed in FPM, must not be confused with the spindle speed of the lathe which is expressed in RPM. To obtain uniform cutting speed, the lathe spindle must be revolved faster for workplaces of small diameter and slower for workplaces of large diameter. The proper cutting speed for a given job depends upon the hardness of the material being machined, the material of the tool bit, and how much feed and depth of cut is required.
Cutting speeds for metal are usually expressed in surface feet per minute, measured on the circumference of the work. Spindle revolutions per minute (RPM) are determined by using the formula: 12 X SFM = RPM 3.1416 X D Which is simplified to: 4 X SFM = RPM D Where SFM is the rated surface feet per minute, also expressed as cutting speed. RPM is the spindle speed in revolutions per minute D is the diameter of the work in inches. In order to use the formula simply insert the cutting speed of the metal and the diameter of the workpiece into the formula and you will have the RPM. Turning a one-half inch piece of aluminum.
Cutting speed of 200 SFM. Would result in the following: 4 x 200 = 1600 RPM 1/21 Table 7-2 in Appendix A lists specific ranges of cutting speeds for turning and threading various materials under normal lathe conditions, using normal feeds and depth of cuts. Note that in Table 7-2 the measurement calculations are in inch and metric measures. The diameter measurements used in these calculations are the actual working diameters that are being machined. And not necessarily the largest diameter of the material.
The cutting speeds have a wide range so that the lower end of the cutting speed range can be used for rough cutting and the higher end for finish cutting. If no cutting speed tables are available, remember that, generally. Hard materials require a slower cutting speed than soft or ductile materials. Materials that are machined dry. Without coolant.
Require a slower cutting speed than operations using coolant. Lathes that are worn and in poor condition will require slower speeds than machines that are in good shape. If carbide-tipped tool bits are being used, speeds can be increased two to three times the speed used for highspeed tool bits. Feed Feed is the term applied to the distance the tool bit advances along the work for each revolution of the lathe spindle. Feed is measured in inches or millimeters per revolution, depending on the lathe used and the operator's system of measurement. Table 3-3 in Appendix A is a guide that can be used to select feed for general roughing and finishing operations.
A light feed must be used on slender and small workplaces to avoid damage. If an irregular finish or chatter marks develop while turning. Reduce the feed and check the tool bit for alignment and sharpness. Regardless of how the work is held in the lathe, the tool should feed toward the headstock. This results in most of the pressure of the cut being put on the work holding device. If the cut must be fed toward the tailstock.
Use light feeds and light cuts to avoid pulling the workpiece loose. Depth of Cut Depth of cut is the distance that the tool bit moves into the work. Usually measured in thousandths of an inch or in millimeters. General machine practice is to use a depth of cut up to five times the rate of feed, such as rough cutting stainless steel using a feed of 0.020 inch per revolution and a depth of cut of 0.100 inch. Which would reduce the diameter by 0.200 inch. If chatter marks or machine noise develops. Reduce the depth of cut.
MICROMETER COLLAR Graduated micrometer collars can be used to accurately measure this tool bit movement to and away from the lathe center axis. The depth of cut can be accurately measured when moving the tool bit on the cross slide by using the cross slide micrometer collar. The compound rest is also equipped with a micrometer collar.

These collars can measure in inches or in millimeters, or they can be equipped with a dual readout collar that has both. Some collars measure the exact tool bit movement. While others are designed to measure the amount of material removed from the workpiece (twice the tool bit movement). Consult the operator's instruction manual for specific information on graduated collar use.
CNC Cutting Speeds Why are cutting speeds so important in CNC, and why are they hard to calculate? First thing's first-if you're just looking for quick access to CNC cutting speeds, the best place to look is at our. Our free 30-day trial will get you calculating your feeds and speeds right away.
If what you're looking for is to learn more about CNC cutting speeds, check out our free. There's a wealth of great information there. If you have a little extra time, and you're curious about the differences between manual cutting speeds and CNC cutting speeds, keep reading. What I want to talk about here, are two things: First, why are cutting speeds so important for CNC, and second, how come they're so much harder to calculate for CNC than they were for manual machines?
A Look Back at the Simpler Life of the Manual Machinist Using a Bridgeport Mill Once upon a time, we had little or no automation. At best, there were hydraulic tracer machines and screw machines.
That's not to say they couldn't do quite a lot, but they certainly were not as ubiquitous as CNC has become in today's machine shops. Instead, we had machines like the iconic. Let's start by taking a look at the good old Bridgeport, copies of which are still being manufactured today.
The heart of any machine tool is its spindle, and for the Bridgeport, the pinnacle of spindle evolution was the 2JS head. That head used a back gear and a variable sheave belt system to achieve reasonably flat distribution of its 2 HP all the way from 50 to 3750 rpm. Its taper was the common-as-cats R8. Not too shabby: 2 HP from 50 to 3750 rpm and an R8 taper! For automation, we had the Mk I revision 1932 through 2011 or later human machinist.
Feedrates were a function of how fast that machinist could turn the handwheel, or in some cases, how fast a power feed could move, which wasn't an awful lot faster. Given that the handwheel moves through 100 0.001' divisions each turn and you could maybe turn 2 or 3 turns a second during roughing, and maybe half that for finishing or less, we're talking feedrates of 6 to maybe 18 inches per minute. In terms of axes, the machinist could move them one at a time-no coordinated motion was really possible without a rotary table, and even then, coordinated motion was limited to circles. The slick interpolated moves of a modern CNC were hardly even a gleam in the imagination.
This was just how these machines worked and nobody worried about it too much. Differences for CNC Machinists Using a Haas Mini-Mill And then along came CNC. For reference, let's consider the smallest Haas CNC mill. I'm not sure this is the most common CNC the way the Bridgeport was the most common manual mill, but it is a fairly common CNC that perhaps most importantly is similar in size and capacity. Here is one that was featured in our: The Haas Mini Mill. Starting with the spindle again, we have a 7.5 HP, 6000 rpm spindle with a CAT40 taper.
The quoted cutting feedrate is 500 inches per minute, and of course this machine is perfectly happy moving not just all 3 axes simultaneously, but also slapping on a 4th axis that will move too! Getting the Most Out of Each Machine Requires a Different Strategy? Given that you've only got 2 HP, 3750 rpm, and maybe 18 inches per minute of feedrate, plus the fact that many would say the limits of the R8 taper are an endmill of about 3/4' maximum diameter, what's the best strategy for removing material with your Bridgeport? Modern CNC's often use fancy toolpath strategies such as constant tool engagement angle paths and they take advantage of geometric effects like radial chip thinning to move extremely quickly while exerting as little force as possible on the machine and working to maintain the life of the tool. There's no point in any of that with the Bridgeport. You can't turn the handwheel fast enough to feed a radial chip thinned path, and you can't turn two handwheels at once to go around a corner without dwelling, let alone manage the complicated curlicues that a constant tool engagement path makes. Comparison of the same pocket done with HSM and conventional toolpaths in GibbsCAM as shown by the.
Neither one could really be done on a manual machine. So, instead of having all this fancy digital sophistication, the answer for manual machinists was to load the biggest cutter they could and bury it. Here's how the cutting speeds and conditions differ: - With much slower spindles and on materials that like fast spindle speeds like aluminum, we rely more on chipload than spindle speed to do the work.
It turns out that because it is less brittle, HSS tooling can take higher chiploads than carbide. Carbide can tolerate much higher spindle speeds that more than offset that difference, but.
Since we have such slow feedrates, it isn't like we can't take great heaping gobs if we're taking skinny little cuts. The answer is to use a larger cutter and bury it. Got a 3/4' endmill?
Use as close to 3/4' width of cut as you can. Since we've buried the width of cut, and we don't have a lot of cut calculation sophistication anyway, we probably aren't cutting too deep. Depths of cut are 1 x Diameter or maybe a little more, but nothing too crazy. I'll add one last consideration-with manual machining, not only are things not happening nearly as quickly as they do with CNC, but the machinist is getting instant feedback from the handwheel about how 'happy' the cut is. Those factors, in a nutshell, radically simplify cutting speeds for manual machining.
With no fancy toolpaths, an inability to feed very quickly, and a need to make shallow but wide cuts, we eliminate a whole host of complications. For this kind of machining, work just fine. In fact, you can basically tune it up by ear pretty easily once you know what a good cut sounds like.
Now We Can See Why Cutting Speeds are Much Harder for CNC! Getting back to the case for CNC, there are a whole host of new factors to consider such as: - Radial chip thinning. Any time you cut less than half the diameter of the cutter wide, the chipload isn't what you calculate with the simple equations. The thinner the slice you're taking, the further off you will be. If the chipload goes too low, your tool will begin to 'rub', and tool life falls off quickly. The likelihood of rubbing while manually machining is much less.
At 3000 rpm and a 3 IPM feedrate, you've still got room to go 3-5x slower before you're into true rubbing territory. HSS tooling is sharper than carbide, making it even harder to get the tool to rub. You're keeping the cut relatively shallow due to the broad widths of cut, and you're not going around corners as fast as a CNC would.
Speeds And Feeds Of Manual Lathe
This greatly improves chip clearing and keeps the big jumps in load on the tool that corners cause from happening so suddenly. The list goes on, but you get the idea. For CNC, the G-Wizard Cutting Speed Calculations consider nearly 50 variables versus the handful that the simple equations are focused on.
In addition to facing more complexity from a physics standpoint, the CNC machinist is cut off from the feel of the machine. When something goes wrong, your first warning is often dire (tool breakage is the least of your worries) and then it's a mad dash for that bright red emergency stop button. Want to Learn More? If you'd like to learn more about the art of calculating CNC cutting speeds, check out our free or get signed up to try the G-Wizard Calculator: No credit card required-just your name and email.